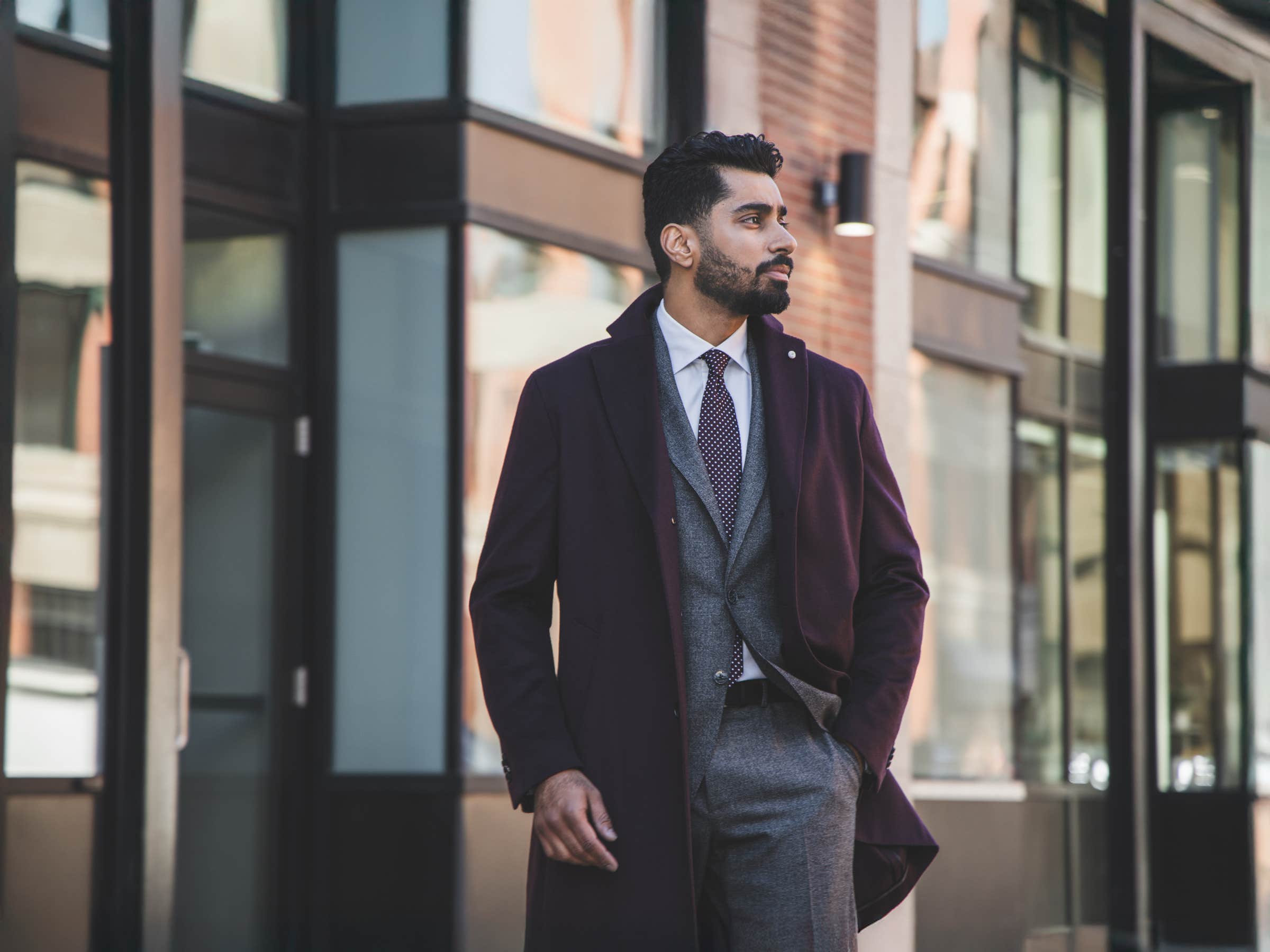
The Helm’s Winter 2024 Outerwear Highlights
Now that winter is in full swing, it’s the perfect time to upgrade your outerwear collection. From more formal pieces to those designed for when you’re on the go, this season's selections offer something for every occasion.
Whether you're braving the cold or simply looking to refresh your winter wardrobe, our Winter 2024 Outerwear Highlights showcase the best in luxury fabrics, design, and craftsmanship.
TOPCOATS
Timeless and elegant, perfect for layering over a suit or sport jacket.
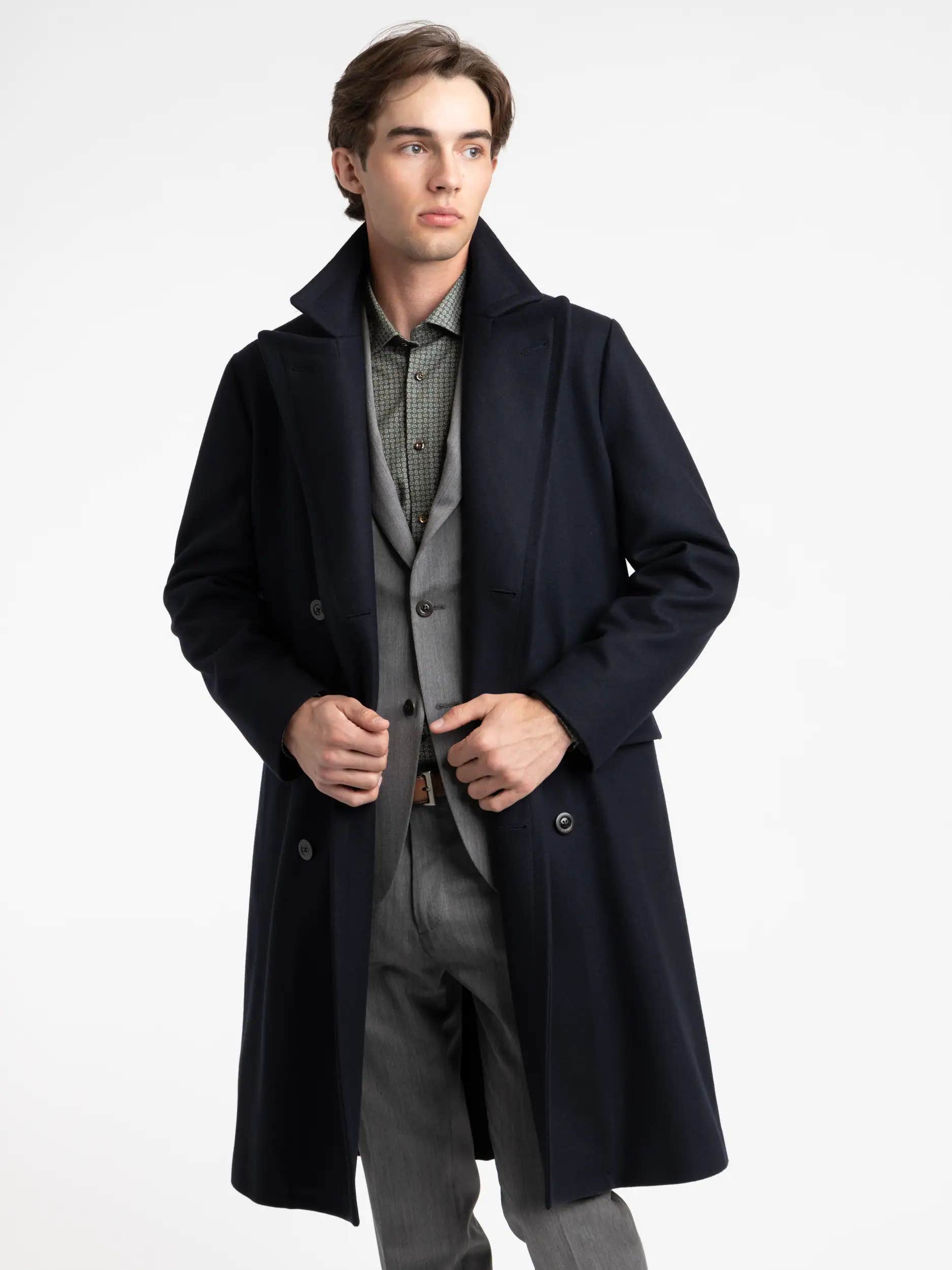
Boglioli | Navy Double-Breasted Topcoat
Made from a virgin wool and cashmere blend, this topcoat features Italian tailoring in a modern oversized cut.
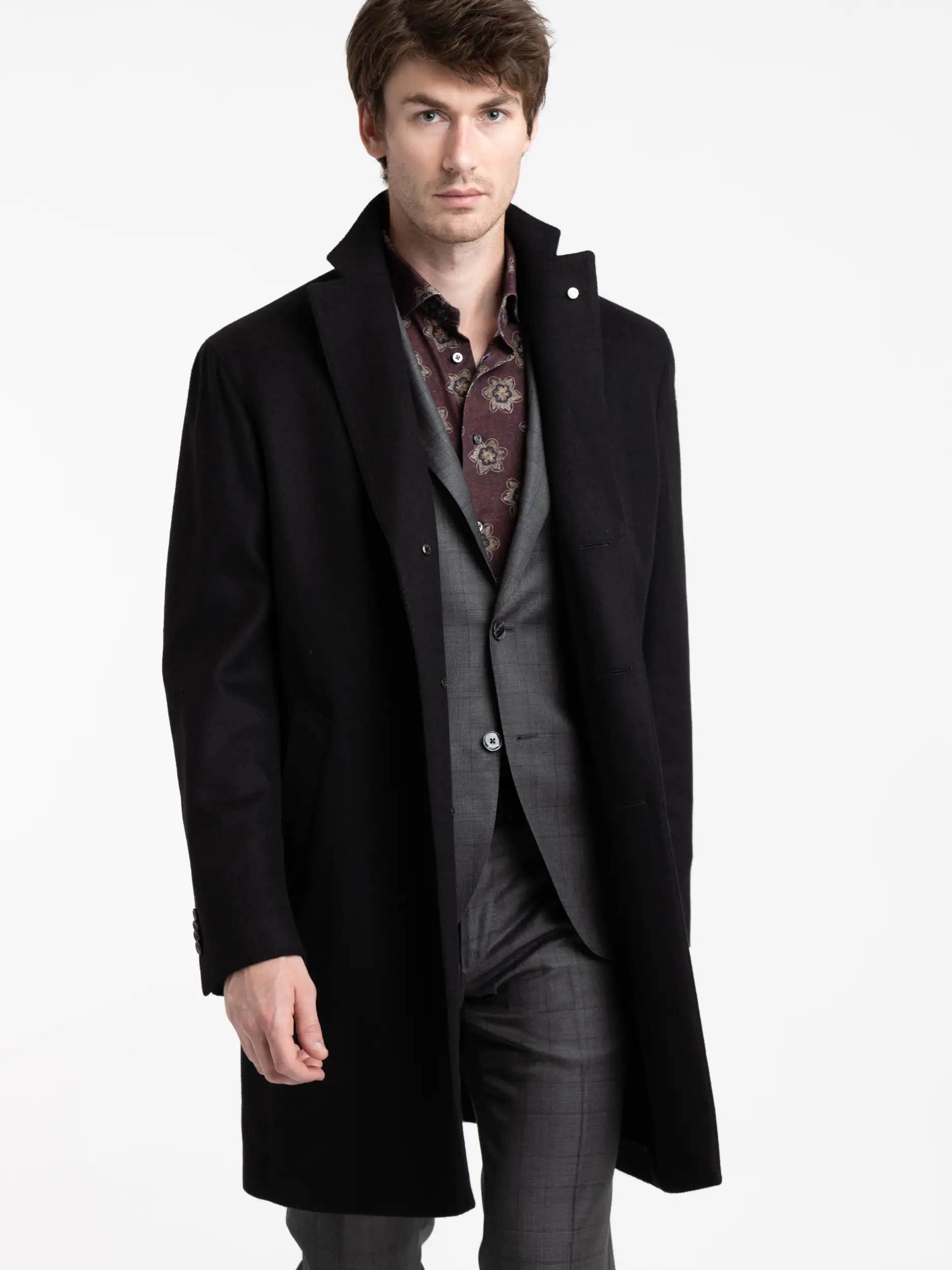
Luigi Bianchi | Black Colombo Thermo Topcoat
Designed in a form-fitting silhouette, this topcoat blends wool and cashmere with a water-resistant finish.
Puffers
Warm, lightweight, and ideal for braving the cold.
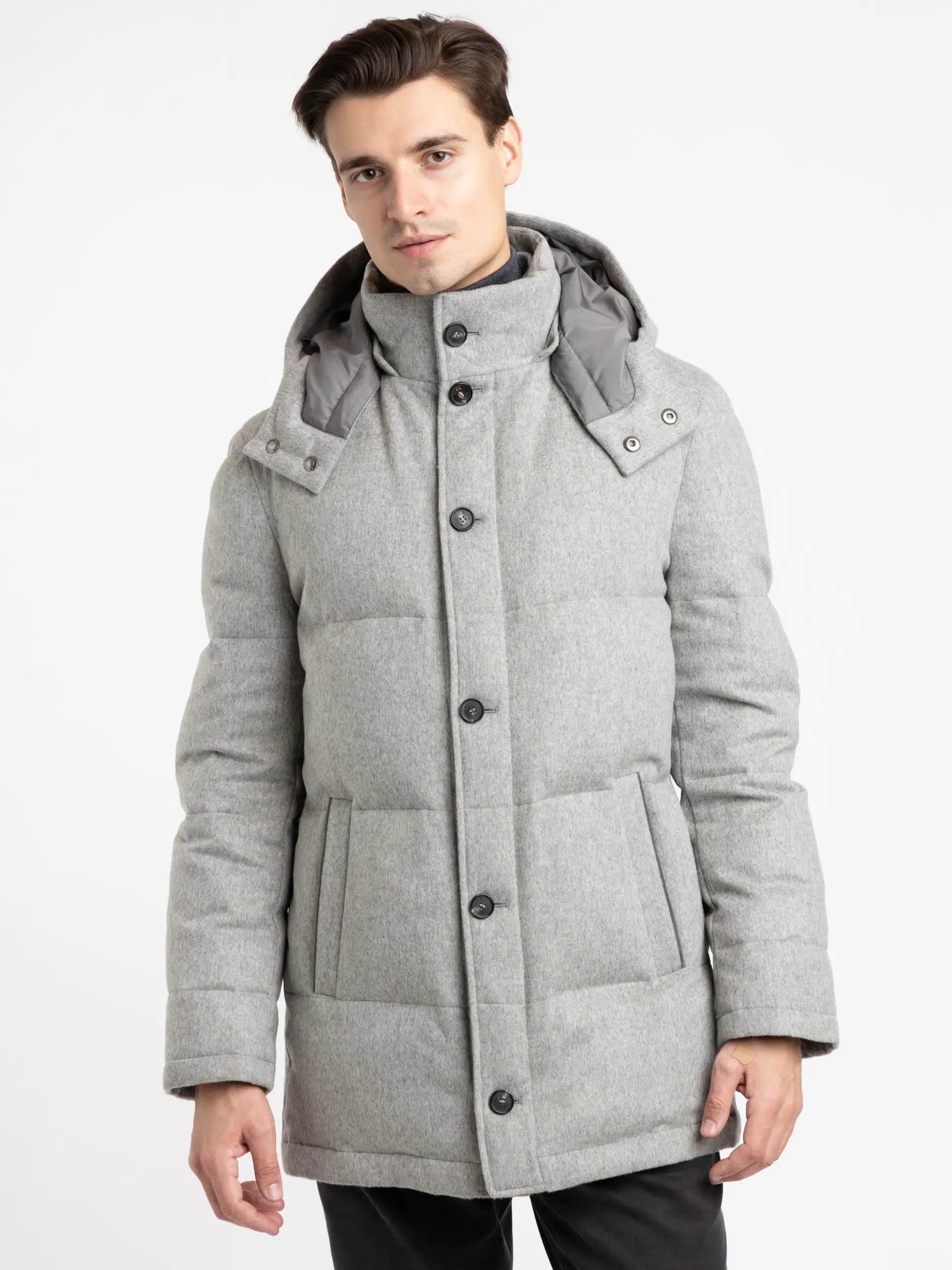
Manto | Light Grey Cashmere Down Puffer
An Italian-crafted puffer with water-repellent cashmere and down filling.

Stone Island | Guibbotto Grey Seamless Tunnel Nylon Down-TC Jacket
Innovatively designed with seamless construction and down insulation for exceptional warmth, durability, and weather resistance.
JACKETS
Durable and insulated, great for everyday wear.
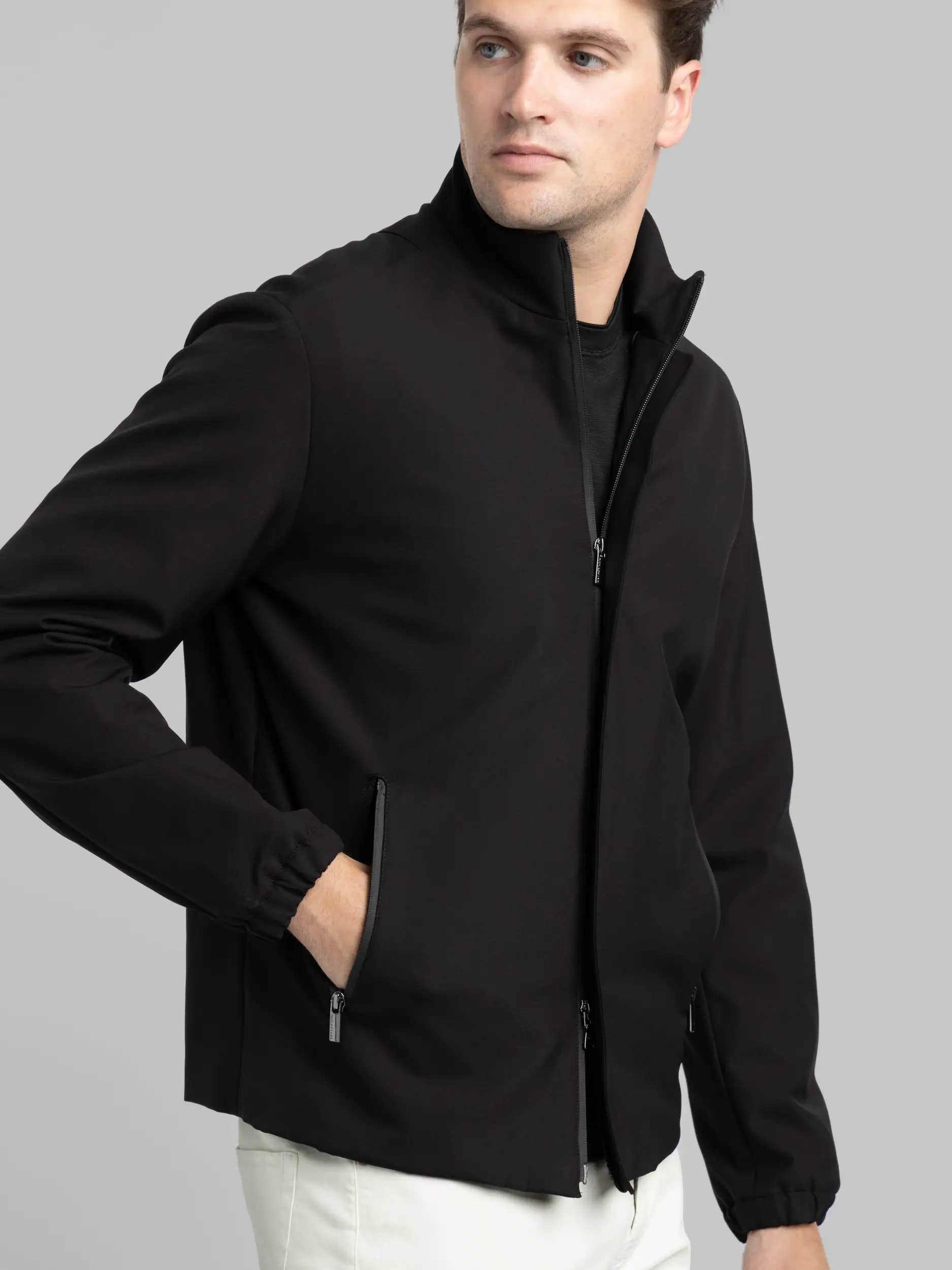
Paul & Shark | Black Full Zip Jacket
Tailored for active lifestyles, this jacket combines stretch fabric with sustainable materials.

Brunello Cucinelli | Brown Fur Collar Aviator Jacket
Featuring an aviator-inspired design, this suede jacket is finished with a soft plush shearling collar and lining.

Paul & Shark | Black Typhoon Platinum Quilted Jacket
Waterproof, windproof, and made with recycled Ecodown®.
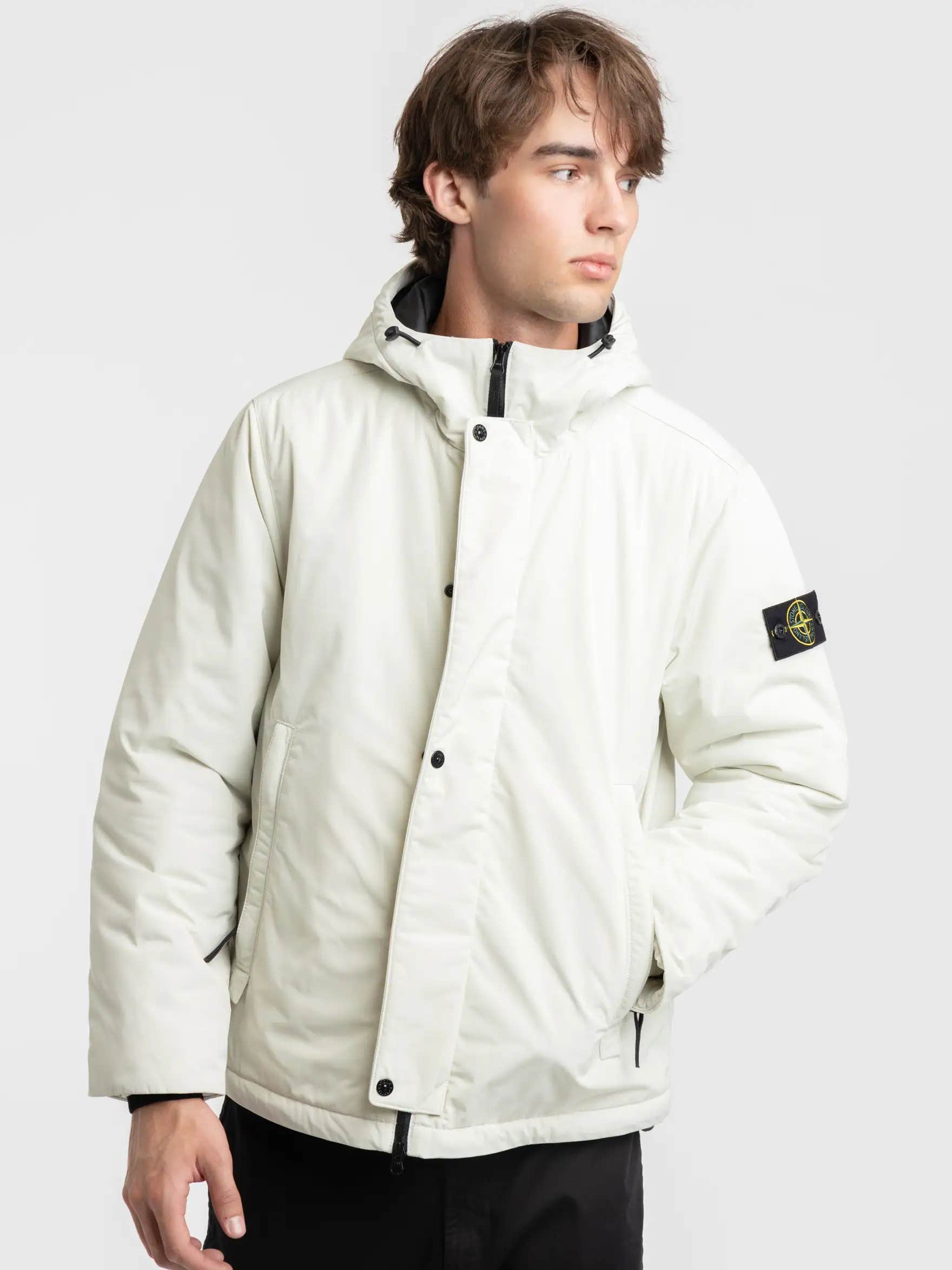
Stone Island | Giubbotto White Micro Twill PrimaLoft® Jacket
Made with recycled PrimaLoft® insulation and water-resistant micro twill, this jacket offers a high warmth-to-weight ratio.

Stone Island | Black Micro Twill PrimaLoft® Raincoat
Integrated with Primaloft® insulation, wind and water-resistant micro twill, this raincoat is finished with a metallic effect.

Brunello Cucinelli | Navy Wool Beaver Cloth Jacket
Crafted from velvety wool with corduroy inserts, this jacket has a soft, fleece-like feel.

Polo Ralph Lauren | Piper Navy Hybrid Full-Zip Mockneck Sweater
This sweater combines a smooth texture with quilted detailing and rib-knit accents.
OVERSHIRTS & VESTS
Practical and versatile, these pieces offer an extra layer of warmth without the bulk.

ZEGNA | Blue Trofeo™ Cashmere Overshirt
Blending extra-long merino fibres with soft cashmere, this tailored overshirt features a sleek zip-up design with a high stand collar.

Polo Ralph Lauren | The Eastham Quilted Utility Vest in Navy
This vest features onion quilting, a down-alternative fill, and suede accents.

04651 / A trip in a bag | Navy Breeze Overshirt
Crafted from windproof, water-repellent microfibre, this lightweight, padded overshirt offers reliable protection against unpredictable weather.
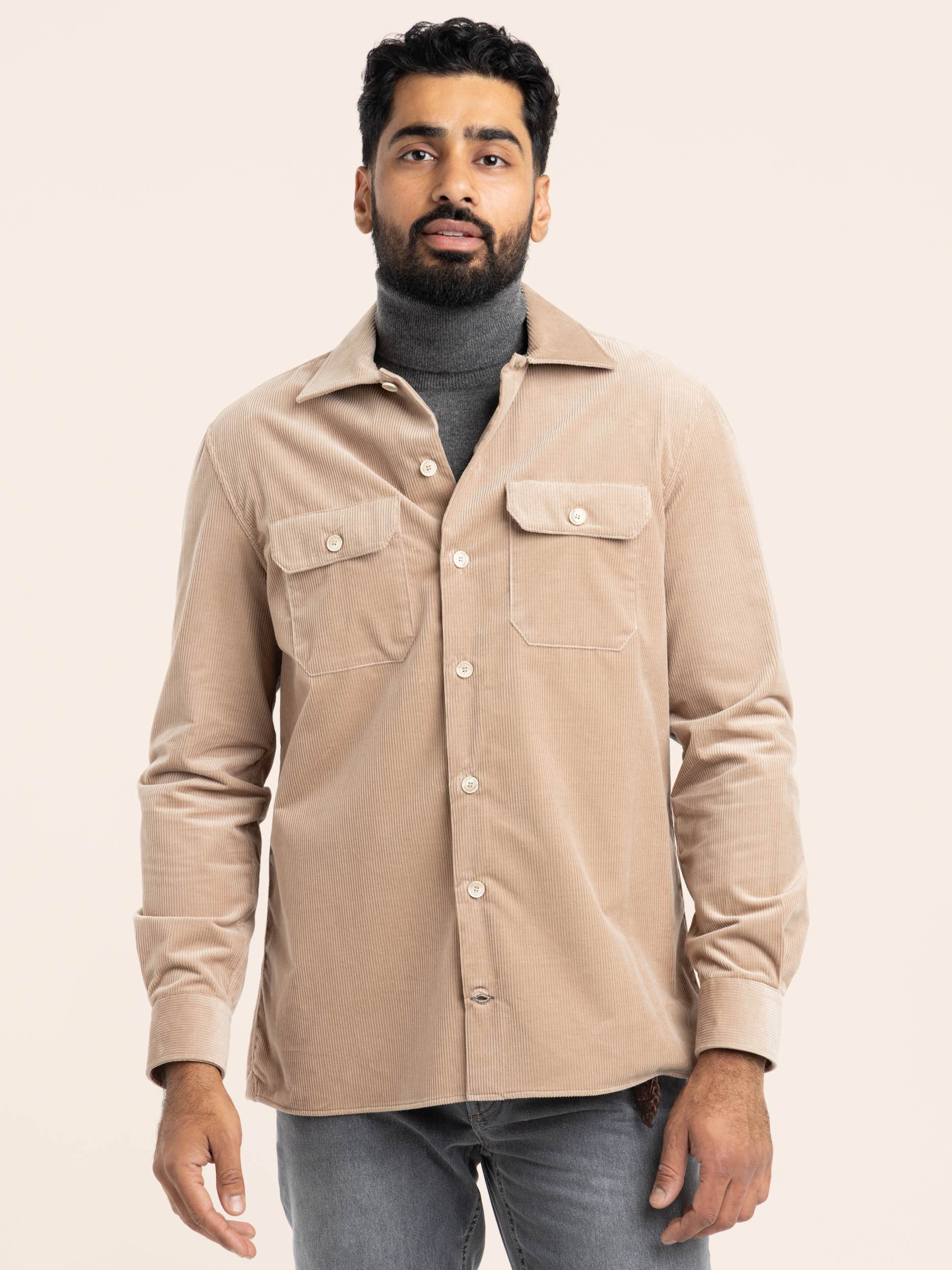
Brunello Cucinelli | Light Brown Corduroy Overshirt
Made with soft cotton corduroy, this overshirt features horn buttons and patch pockets.
We understand that things don't always work out. We offer easy returns in-store or by mail.
Come see the product up close at our Flagship Store.
For local orders, in-store pickup is available for no cost.
Your clothing should always represent you well, whether you bought it yesterday or 5 years ago.
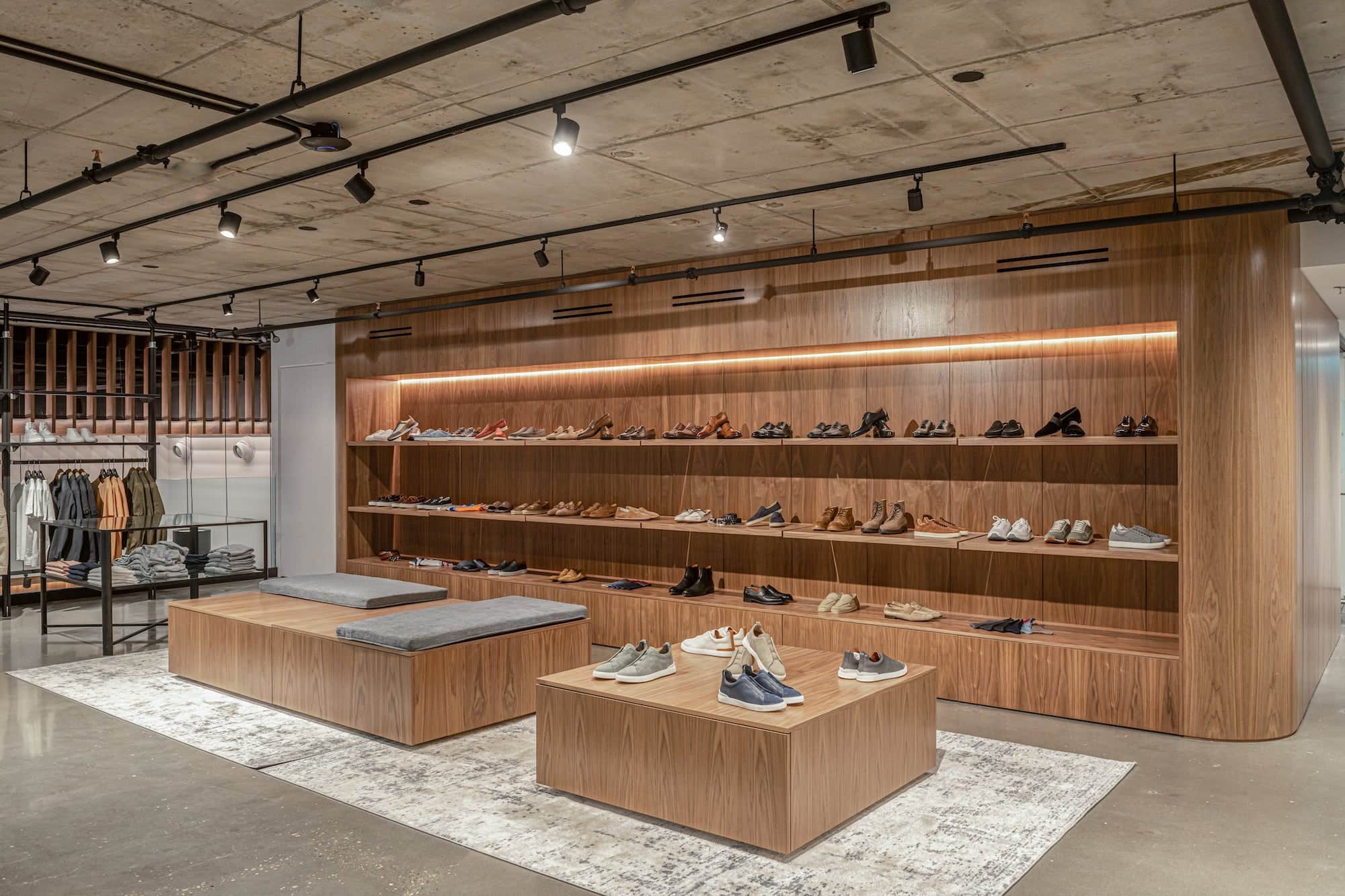
The Flagship
Our brand new flagship store in Edmonton, Alberta is now open to serve you! In our mission to provide Edmonton with an elevated experience, our vision for this store was something spanning multiple floors with a unique experience on every level.